Our patented technology is one of a kind, revolutionizing methods of recycling waste rubber in order to manufacture eco-friendly, high-quality, and inexpensive synthetic rubber for use in a wide range of products and specialty markets.
The EcoTech recycling plant uses a combination of mechanical shredding and granulation machines as well as a semi-cryogenic pulverization system. The company’s technology freezes the rubber granules without the use of liquid nitrogen, enabling the rubber to be milled into ultra-fine powders and efficiently separated from other impurities.

Active Rubber Manufacturing Process
iso-certified 4001 & 9001

Receiving Raw Materials
Obtaining rubber crumbs (1.8cm) from old tires, cleaned of metals and fibers.

Freezing
(Patented technology)
The rubber crumbs are inserted into a proprietary freezer and semi-cryogenically frozen to =70 degrees C. No chemical agents are used, thus keeping the rubber qualities intact.

Milling
Rubber is then grounded to an ultra-fine rubber powder (averaging 100-120 microns per granule in size).

Filtering
(Patented technology)
Problematic to any application, the remaining textiles are separated and removed in order to yield ultra-fine rubber powder.

Mixing
(Patented technology)
The mixing process within the Banbury rubber mixer, combined with EcoTech’s proprietary chemical formulation, enables the activation process that creates Active Rubber.

Pressing
The rubber leaves the mixer where it is pressed into sheets.
Cooling & Packing
The sheets are cooled by a fan and placed on a platform or pallet for packing.
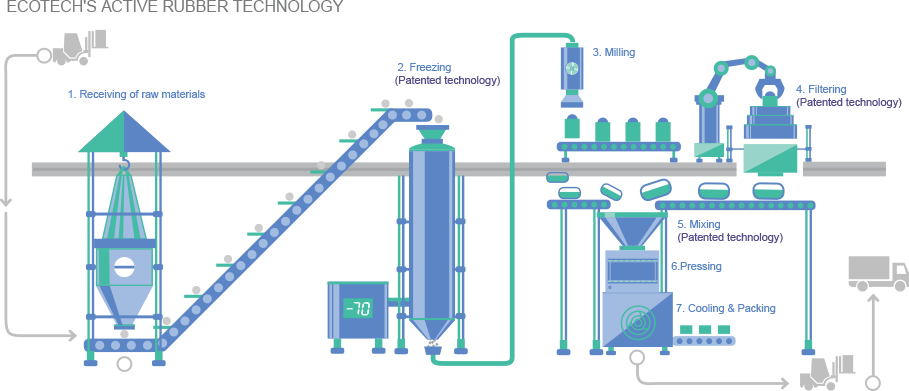